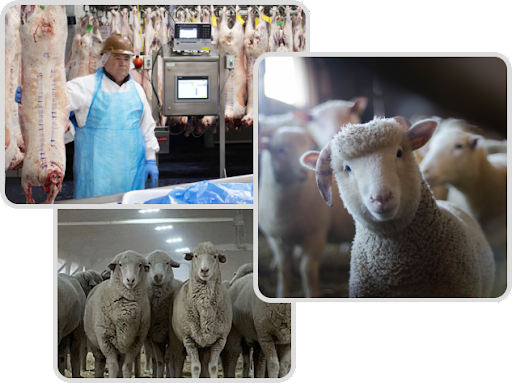
About
The Comapny
A renowned market leader in the meatpacking industry with more than 1000 family ranch partners, the company is a lamb processing plant spread across four locations in the United States. Having recently unveiled the “greenest” lamb plant in the United States, it is known for being extremely vigilant about animal welfare, managing data efficiently, and maintaining traceability.